How to Prevent Costly Downtime With Regular Inspections: Fleet Brake Maintenance
Learn how regular fleet brake maintenance prevents costly downtime, ensures safety, and keeps your trucks on the road. Explore inspection tips and best practices.
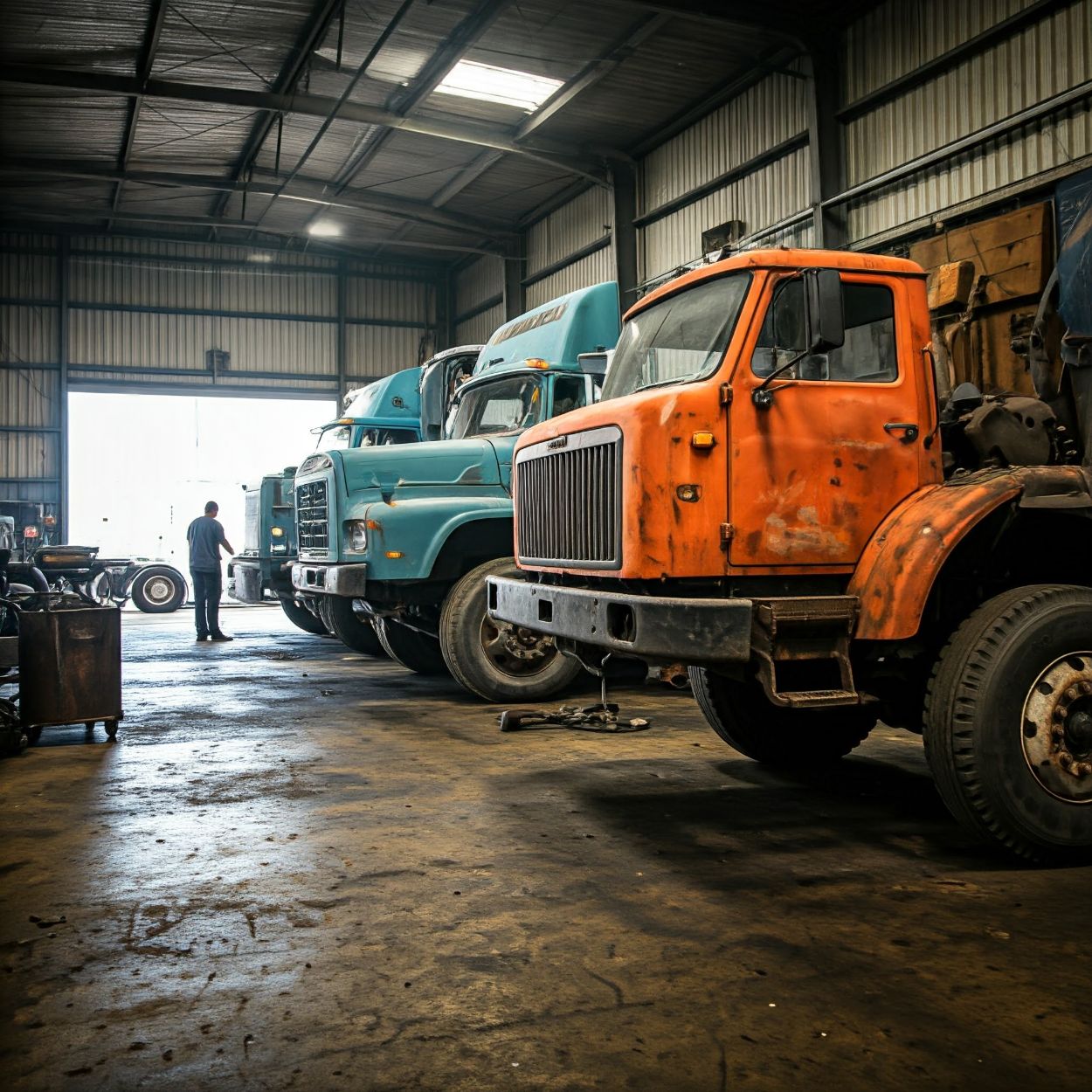
When it comes to keeping your fleet rolling smoothly and minimizing costly downtime, brake maintenance is essential. Neglecting regular inspections and upkeep can lead to expensive repairs and even pose a safety risk. As the backbone of your truck's safety system, brakes need to be in top condition, especially in a fleet operating day in and day out on demanding routes. By staying on top of brake maintenance, you can extend the life of your vehicles and ensure your fleet remains safe and efficient.
Understanding Brake Systems in Heavy-Duty Trucks
Heavy-duty truck brake systems differ significantly from those in passenger vehicles. Fleet trucks rely on compressed air, rather than hydraulics, to power their brakes. These air brakes are composed of multiple key components such as air compressors, air dryers, and compressed air tanks. At the business end, there are the brake shoes, S-cams, and slack adjusters that directly engage the brakes and bring rigs to a stop.
Given the complexity of these systems, small issues can quickly snowball into major problems if not detected early. For this reason, regular fleet brake maintenance inspections are key to identifying minor wear-and-tear issues before they escalate into major brake failures.
The Importance of Regular Inspections
One of the most effective ways to prevent brake failures is through consistent and scheduled brake system inspections. The typical lifespan of brake components varies depending on driving conditions, weight loads, and climate factors, but waiting until they wear down completely can lead to expensive repairs—not to mention the risk of accidents.
Basic Inspection of Terminals (BIT) inspections, which are mandated every 90 days for commercial fleets, should be adhered to strictly. This rigorous schedule ensures that fleets are always up to code and provides a chance to catch any minor issues before they turn into costly downtime.
What Regular Brake Maintenance Entails
To prevent costly downtime, routine brake inspections should focus on several critical components:
- Brake Shoes and Drums: These are the surfaces that generate friction, slowing down the truck. Excessive wear can lead to cracks or even complete failure. Regularly checking the thickness of brake shoes and the condition of the brake drums ensures the system can continue functioning safely.
- Air Lines and Compressors: Inspect for leaks or signs of wear that can compromise the air pressure needed to activate the brakes. Faulty air compressors or damaged air lines can reduce brake responsiveness, especially under heavy loads.
- Slack Adjusters: These help maintain the proper clearance between the brake shoes and the drum. Improperly adjusted slack adjusters can lead to inefficient braking, and, in severe cases, brake failure.
- S-cams: Regular inspections ensure that the S-cam, which presses the brake shoes against the drum, is rotating freely and without excess wear.
- Air Dryers: These remove moisture from the compressed air before it enters the brake system. If moisture builds up, it can lead to freezing or corrosion, both of which are disastrous for brake functionality.
Best Practices for Fleet Brake Maintenance
- Daily Inspections: Drivers should conduct basic checks daily, ensuring there are no obvious signs of wear or damage. This includes listening for unusual sounds and checking air pressure levels.
- Scheduled Professional Inspections: Every 90 days, a more thorough inspection should be performed by a trained technician. This will cover every component, from the air compressor to the brake shoes.
- Keeping Accurate Maintenance Records: Detailed records of all inspections and repairs allow fleet managers to track the wear patterns and predict when maintenance will be needed. This helps prevent costly downtime by addressing issues proactively rather than reactively.
- Use of High-Quality Parts: Using OEM-quality parts during maintenance ensures the longevity of your brake system. Subpar components may save money upfront but could cost much more in the long run due to frequent replacements or unexpected failures.
- Brake System Testing: Regularly performing brake system tests ensures that every part is working cohesively. This includes monitoring air pressure stability, brake balance, and overall system performance.
The Risks of Neglecting Brake Maintenance
Ignoring regular inspections can lead to catastrophic failures that not only result in costly repairs but can also put drivers and others on the road at risk. Without proper fleet brake maintenance, you may face issues such as:
- Overheating Brakes: This can occur when brake shoes or drums wear too thin, causing excess friction. It reduces braking power and can damage the entire brake system.
- Air Compressor Failure: A malfunctioning air compressor can leave your entire brake system without the power needed to function properly. This leads to ineffective braking and potential accidents.
- Brake Line Leaks: If a leak develops in the air lines, it can reduce brake effectiveness or cause a complete failure, particularly under heavy loads or in emergency situations.
- Increased Downtime: When brakes fail, repairs often involve taking trucks off the road for extended periods, resulting in costly downtime. These repairs can be expensive and impact delivery schedules.
Learn More
Preventing costly downtime is achievable with regular and proactive brake maintenance. By implementing a consistent schedule of inspections and maintenance for your fleet brake systems, you can avoid unexpected failures and keep your trucks on the road, delivering goods safely and on time. Ensure your fleet brake maintenance is a priority and your trucks will continue to perform efficiently for the long haul.
For fleet managers looking to stay ahead of brake issues, partnering with a professional shop like Better Repair in Philadelphia, PA, and Fort Lauderdale, FL, is a crucial step toward maintaining fleet efficiency and safety.
More Articles
Contact Us
Need a mobile repair, have questions, or looking for roadside assistance within Fort Lauderdale, FL? Get in touch, we're open Monday through Friday from 8:00am to 5:00pm and Saturday from 8:00am to 2:00pm.